Teknologi dadu wafer, sebagai langkah kritikal dalam proses pembuatan semikonduktor, dikaitkan secara langsung dengan prestasi cip, hasil dan kos pengeluaran.
#01 Latar Belakang dan Kepentingan Dicing Wafer
1.1 Definisi Dicing Wafer
Pembuatan dadu wafer (juga dikenali sebagai scribing) ialah langkah penting dalam pembuatan semikonduktor, bertujuan untuk membahagikan wafer yang diproses kepada beberapa die individu. Die ini biasanya mengandungi kefungsian litar lengkap dan merupakan komponen teras yang akhirnya digunakan dalam pengeluaran peranti elektronik. Apabila reka bentuk cip menjadi lebih kompleks dan dimensi terus mengecil, keperluan ketepatan dan kecekapan untuk teknologi dadu wafer menjadi semakin ketat.
Dalam operasi praktikal, dadu wafer biasanya menggunakan alat berketepatan tinggi seperti bilah berlian untuk memastikan setiap dadu kekal utuh dan berfungsi sepenuhnya. Langkah-langkah utama termasuk penyediaan sebelum pemotongan, kawalan tepat semasa proses pemotongan, dan pemeriksaan kualiti selepas pemotongan.
Sebelum memotong, wafer mesti ditanda dan diletakkan untuk memastikan laluan pemotongan yang tepat. Semasa pemotongan, parameter seperti tekanan dan kelajuan alat mesti dikawal dengan ketat untuk mengelakkan kerosakan pada wafer. Selepas pemotongan, pemeriksaan kualiti menyeluruh dijalankan untuk memastikan setiap cip memenuhi piawaian prestasi.
Prinsip asas teknologi pemotongan wafer bukan sahaja merangkumi pemilihan peralatan pemotongan dan penetapan parameter proses tetapi juga pengaruh sifat mekanikal dan ciri bahan terhadap kualiti pemotongan. Sebagai contoh, wafer silikon dielektrik rendah k, disebabkan sifat mekanikalnya yang rendah, sangat terdedah kepada kepekatan tegasan semasa pemotongan, yang membawa kepada kegagalan seperti serpihan dan keretakan. Kekerasan dan kerapuhan rendah bahan rendah-k menjadikannya lebih terdedah kepada kerosakan struktur di bawah daya mekanikal atau tekanan haba, terutamanya semasa pemotongan. Sentuhan antara alat dan permukaan wafer, ditambah dengan suhu tinggi, boleh memburukkan lagi kepekatan tegasan.
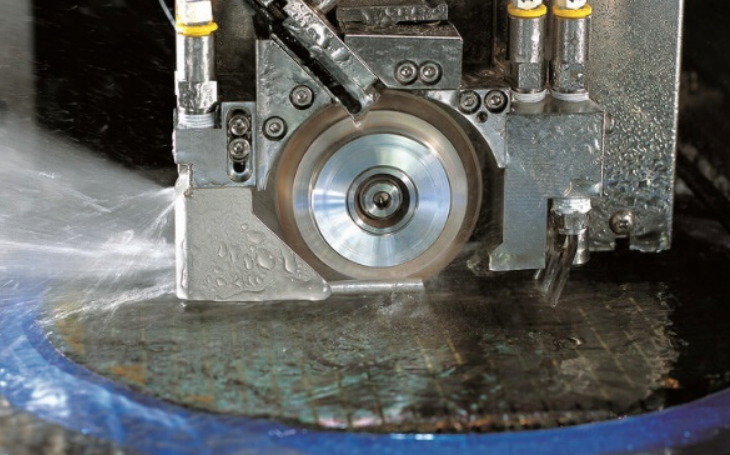
Dengan kemajuan dalam sains bahan, teknologi pemotongan wafer telah berkembang melangkaui semikonduktor berasaskan silikon tradisional untuk memasukkan bahan baharu seperti galium nitrida (GaN). Bahan-bahan baharu ini, disebabkan kekerasan dan sifat strukturnya, menimbulkan cabaran baharu untuk proses memotong dadu, yang memerlukan penambahbaikan selanjutnya dalam alat dan teknik pemotongan.
Sebagai proses kritikal dalam industri semikonduktor, dadu wafer terus dioptimumkan sebagai tindak balas kepada permintaan yang berkembang dan kemajuan teknologi, meletakkan asas untuk mikroelektronik masa depan dan teknologi litar bersepadu.
Penambahbaikan dalam teknologi pemotongan wafer melangkaui pembangunan bahan dan alatan tambahan. Ia juga merangkumi pengoptimuman proses, peningkatan dalam prestasi peralatan, dan kawalan tepat parameter dicing. Kemajuan ini bertujuan untuk memastikan ketepatan tinggi, kecekapan dan kestabilan dalam proses dadu wafer, memenuhi keperluan industri semikonduktor untuk dimensi yang lebih kecil, penyepaduan yang lebih tinggi dan struktur cip yang lebih kompleks.
kawasan penambahbaikan | Langkah-langkah Khusus | Kesan |
Pengoptimuman Proses | - Tingkatkan persediaan awal, seperti kedudukan wafer dan perancangan laluan yang lebih tepat. | - Kurangkan ralat pemotongan dan tingkatkan kestabilan. |
- Kurangkan ralat pemotongan dan tingkatkan kestabilan. | - Gunakan mekanisme pemantauan dan maklum balas masa nyata untuk melaraskan tekanan, kelajuan dan suhu alat. | |
- Rendahkan kadar pecah wafer dan tingkatkan kualiti cip. | ||
Peningkatan Prestasi Peralatan | - Gunakan sistem mekanikal berketepatan tinggi dan teknologi kawalan automasi termaju. | - Meningkatkan ketepatan pemotongan dan mengurangkan pembaziran bahan. |
- Memperkenalkan teknologi pemotongan laser yang sesuai untuk wafer bahan kekerasan tinggi. | - Meningkatkan kecekapan pengeluaran dan mengurangkan ralat manual. | |
- Tingkatkan automasi peralatan untuk pemantauan dan pelarasan automatik. | ||
Kawalan Parameter Tepat | - Laraskan parameter seperti kedalaman pemotongan, kelajuan, jenis alat dan kaedah penyejukan. | - Memastikan integriti die dan prestasi elektrik. |
- Sesuaikan parameter berdasarkan bahan wafer, ketebalan dan struktur. | - Tingkatkan kadar hasil, kurangkan sisa bahan dan kos pengeluaran yang lebih rendah. | |
Kepentingan Strategik | - Meneroka laluan teknologi baharu secara berterusan, mengoptimumkan proses dan meningkatkan keupayaan peralatan untuk memenuhi permintaan pasaran. | - Meningkatkan hasil dan prestasi pembuatan cip, menyokong pembangunan bahan baharu dan reka bentuk cip termaju. |
1.2 Kepentingan Dicing Wafer
Pemotongan wafer memainkan peranan penting dalam proses pembuatan semikonduktor, secara langsung memberi kesan kepada langkah seterusnya serta kualiti dan prestasi produk akhir. Kepentingannya boleh diperincikan seperti berikut:
Pertama, ketepatan dan ketekalan pemotongan dadu adalah kunci untuk memastikan hasil dan kebolehpercayaan cip. Semasa pembuatan, wafer menjalani pelbagai langkah pemprosesan untuk membentuk banyak struktur litar yang rumit, yang mesti dibahagikan dengan tepat kepada cip individu (mati). Jika terdapat ralat ketara dalam penjajaran atau pemotongan semasa proses dadu, litar mungkin rosak, menjejaskan kefungsian dan kebolehpercayaan cip. Oleh itu, teknologi dadu berketepatan tinggi bukan sahaja memastikan integriti setiap cip tetapi juga menghalang kerosakan pada litar dalaman, meningkatkan kadar hasil keseluruhan.
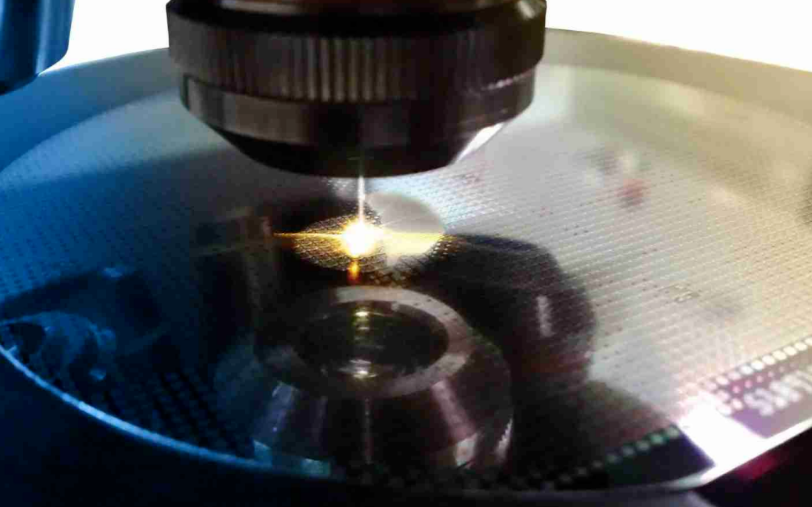
Kedua, pemotongan wafer mempunyai impak yang besar terhadap kecekapan pengeluaran dan kawalan kos. Sebagai langkah penting dalam proses pembuatan, kecekapannya secara langsung mempengaruhi kemajuan langkah seterusnya. Dengan mengoptimumkan proses dadu, meningkatkan tahap automasi, dan meningkatkan kelajuan pemotongan, kecekapan pengeluaran keseluruhan boleh dipertingkatkan dengan sangat baik.
Sebaliknya, pembaziran bahan semasa memotong dadu adalah faktor kritikal dalam pengurusan kos. Menggunakan teknologi dadu termaju bukan sahaja mengurangkan kehilangan bahan yang tidak perlu semasa proses pemotongan tetapi juga meningkatkan penggunaan wafer, sekali gus mengurangkan kos pengeluaran.
Dengan kemajuan dalam teknologi semikonduktor, diameter wafer terus meningkat, dan ketumpatan litar meningkat dengan sewajarnya, meletakkan permintaan yang lebih tinggi pada teknologi dadu. Wafer yang lebih besar memerlukan kawalan yang lebih tepat bagi laluan pemotongan, terutamanya dalam kawasan litar berketumpatan tinggi, di mana penyimpangan kecil pun boleh menyebabkan berbilang cip rosak. Selain itu, wafer yang lebih besar melibatkan lebih banyak garis pemotongan dan langkah proses yang lebih kompleks, memerlukan penambahbaikan selanjutnya dalam ketepatan, konsistensi dan kecekapan teknologi dadu untuk menghadapi cabaran ini.
1.3 Proses Dicing Wafer
Proses dadu wafer merangkumi semua langkah dari fasa penyediaan hingga pemeriksaan kualiti akhir, dengan setiap peringkat adalah kritikal untuk memastikan kualiti dan prestasi cip dadu. Di bawah adalah penerangan terperinci bagi setiap fasa.
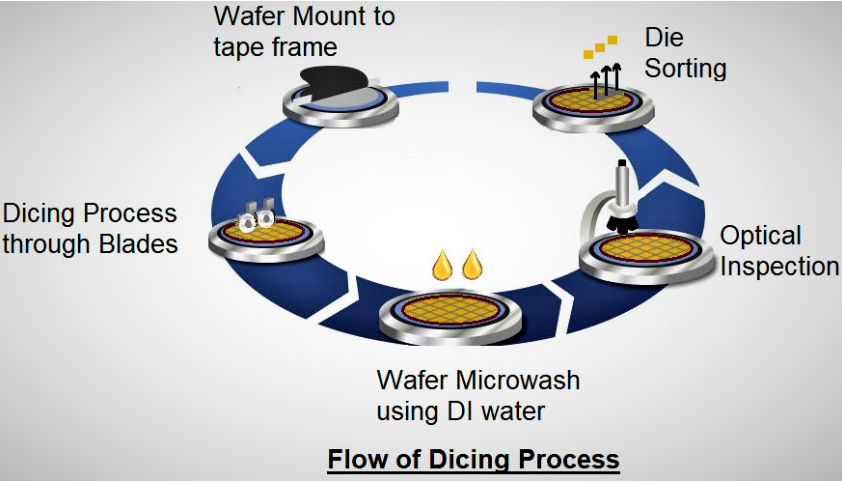
fasa | Penerangan Terperinci |
Fasa Persediaan | -Pembersihan Wafer: Gunakan air ketulenan tinggi dan agen pembersih khusus, digabungkan dengan penyental ultrasonik atau mekanikal, untuk membuang kekotoran, zarah dan bahan cemar, memastikan permukaan bersih. -Kedudukan Tepat: Gunakan peralatan berketepatan tinggi untuk memastikan wafer dibahagikan dengan tepat di sepanjang laluan pemotongan yang direka bentuk. -Penetapan Wafer: Lekatkan wafer pada bingkai pita untuk mengekalkan kestabilan semasa pemotongan, mengelakkan kerosakan akibat getaran atau pergerakan. |
Fasa Pemotongan | -Memotong Bilah: Gunakan bilah bersalut berlian berputar berkelajuan tinggi untuk pemotongan fizikal, sesuai untuk bahan berasaskan silikon dan kos efektif. -Laser Dicing: Gunakan pancaran laser bertenaga tinggi untuk pemotongan tanpa sentuhan, sesuai untuk bahan rapuh atau kekerasan tinggi seperti galium nitrida, menawarkan ketepatan yang lebih tinggi dan kehilangan bahan yang lebih sedikit. -Teknologi Baharu: Memperkenalkan teknologi pemotongan laser dan plasma untuk meningkatkan lagi kecekapan dan ketepatan sambil meminimumkan zon yang terjejas haba. |
Fasa Pembersihan | - Gunakan air ternyahion (air DI) dan agen pembersih khusus, digabungkan dengan pembersihan ultrasonik atau semburan, untuk membuang serpihan dan habuk yang terhasil semasa pemotongan, menghalang sisa daripada menjejaskan proses berikutnya atau prestasi elektrik cip. - Air DI ketulenan tinggi mengelak daripada memperkenalkan bahan cemar baharu, memastikan persekitaran wafer yang bersih. |
Fasa Pemeriksaan | -Pemeriksaan Optik: Gunakan sistem pengesanan optik yang digabungkan dengan algoritma AI untuk mengenal pasti kecacatan dengan cepat, memastikan tiada keretakan atau serpihan pada cip yang dipotong dadu, meningkatkan kecekapan pemeriksaan dan mengurangkan ralat manusia. -Pengukuran Dimensi: Sahkan bahawa dimensi cip memenuhi spesifikasi reka bentuk. -Ujian Prestasi Elektrik: Pastikan prestasi elektrik cip kritikal memenuhi piawaian, menjamin kebolehpercayaan dalam aplikasi seterusnya. |
Fasa Isih | - Gunakan lengan robot atau cawan sedutan vakum untuk mengasingkan cip yang layak daripada bingkai pita dan menyusunnya secara automatik berdasarkan prestasi, memastikan kecekapan dan fleksibiliti pengeluaran sambil meningkatkan ketepatan. |
Proses pemotongan wafer melibatkan pembersihan wafer, kedudukan, pemotongan, pembersihan, pemeriksaan dan pengasingan, dengan setiap langkah adalah kritikal. Dengan kemajuan dalam automasi, pemotongan laser dan teknologi pemeriksaan AI, sistem pemotongan wafer moden boleh mencapai ketepatan, kelajuan dan kehilangan bahan yang lebih rendah. Pada masa hadapan, teknologi pemotongan baharu seperti laser dan plasma akan menggantikan pemotongan bilah tradisional secara beransur-ansur untuk memenuhi keperluan reka bentuk cip yang semakin kompleks, seterusnya memacu pembangunan proses pembuatan semikonduktor.
Teknologi Pemotong Wafer dan Prinsipnya
Imej itu menggambarkan tiga teknologi pemotongan wafer biasa:Memotong Bilah,Laser Dicing, danDicing Plasma. Di bawah adalah analisis terperinci dan penjelasan tambahan mengenai ketiga-tiga teknik ini:
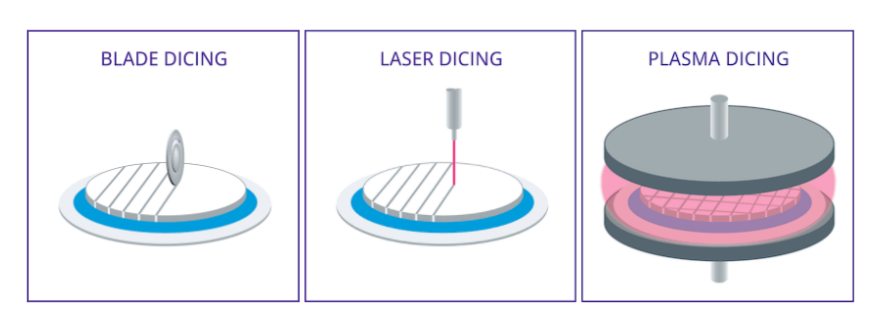
Dalam pembuatan semikonduktor, pemotongan wafer merupakan langkah penting yang memerlukan pemilihan kaedah pemotongan yang sesuai berdasarkan ketebalan wafer. Langkah pertama ialah menentukan ketebalan wafer. Jika ketebalan wafer melebihi 100 mikron, pemotongan pisau boleh dipilih sebagai kaedah pemotongan. Jika dadu bilah tidak sesuai, kaedah dadu patah boleh digunakan, yang merangkumi kedua-dua teknik pemotongan juru tulis dan dadu bilah.
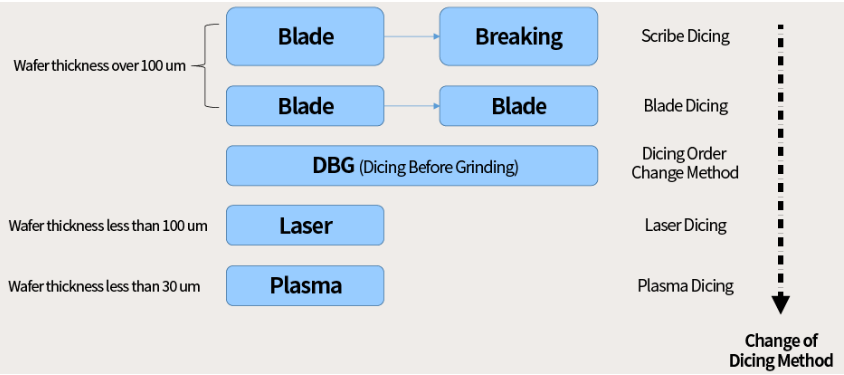
Apabila ketebalan wafer adalah antara 30 dan 100 mikron, kaedah DBG (Dadu Sebelum Pengisaran) disyorkan. Dalam kes ini, pemotongan juru tulis, pemotongan bilah, atau pelarasan urutan pemotongan mengikut keperluan boleh dipilih untuk mencapai hasil yang terbaik.
Untuk wafer ultra-nipis dengan ketebalan kurang daripada 30 mikron, pemotongan laser menjadi kaedah pilihan kerana keupayaannya untuk memotong wafer nipis dengan tepat tanpa menyebabkan kerosakan yang berlebihan. Jika pemotongan laser tidak dapat memenuhi keperluan khusus, pemotongan plasma boleh digunakan sebagai alternatif. Carta alir ini menyediakan laluan membuat keputusan yang jelas untuk memastikan teknologi pemotongan wafer yang paling sesuai dipilih dalam keadaan ketebalan yang berbeza.
2.1 Teknologi Pemotong Mekanikal
Teknologi pemotongan mekanikal adalah kaedah tradisional dalam dadu wafer. Prinsip terasnya ialah menggunakan roda pengisar berlian berputar berkelajuan tinggi sebagai alat pemotong untuk menghiris wafer. Peralatan utama termasuk gelendong galas udara, yang memacu alat roda pengisar berlian pada kelajuan tinggi untuk melakukan pemotongan atau alur yang tepat di sepanjang laluan pemotongan yang telah ditetapkan. Teknologi ini digunakan secara meluas dalam industri kerana kosnya yang rendah, kecekapan tinggi, dan kebolehgunaan yang luas.
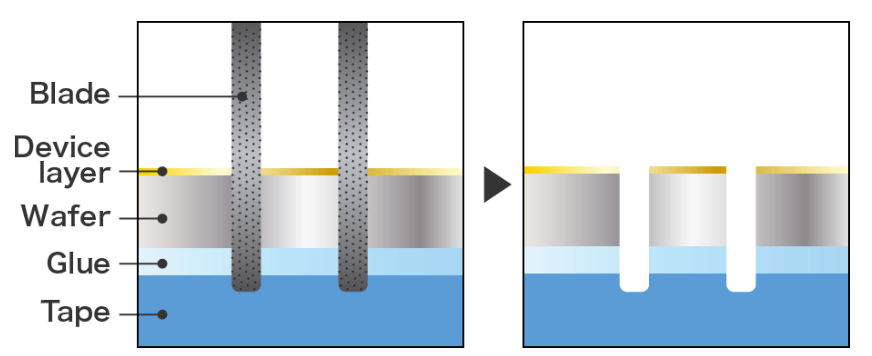
Kelebihan
Kekerasan tinggi dan rintangan haus alat roda pengisar berlian membolehkan teknologi pemotongan mekanikal menyesuaikan diri dengan keperluan pemotongan pelbagai bahan wafer, sama ada bahan berasaskan silikon tradisional atau semikonduktor kompaun yang lebih baru. Operasinya mudah, dengan keperluan teknikal yang agak rendah, seterusnya mempromosikan popularitinya dalam pengeluaran besar-besaran. Selain itu, berbanding kaedah pemotongan lain seperti pemotongan laser, pemotongan mekanikal mempunyai kos yang lebih terkawal, menjadikannya sesuai untuk keperluan pengeluaran volum tinggi.
Had
Walaupun banyak kelebihannya, teknologi pemotongan mekanikal juga mempunyai batasan. Pertama, disebabkan oleh sentuhan fizikal antara alat dan wafer, ketepatan pemotongan agak terhad, selalunya membawa kepada sisihan dimensi yang boleh menjejaskan ketepatan pembungkusan dan ujian cip berikutnya. Kedua, kecacatan seperti serpihan dan rekahan boleh berlaku dengan mudah semasa proses pemotongan mekanikal, yang bukan sahaja menjejaskan kadar hasil tetapi juga boleh menjejaskan kebolehpercayaan dan jangka hayat cip secara negatif. Kerosakan akibat tekanan mekanikal amat memudaratkan pembuatan cip berketumpatan tinggi, terutamanya apabila memotong bahan rapuh, di mana isu ini lebih menonjol.
Penambahbaikan Teknologi
Untuk mengatasi batasan ini, penyelidik terus mengoptimumkan proses pemotongan mekanikal. Penambahbaikan utama termasuk meningkatkan reka bentuk dan pemilihan bahan roda pengisar untuk meningkatkan ketepatan pemotongan dan ketahanan. Selain itu, mengoptimumkan reka bentuk struktur dan sistem kawalan peralatan pemotongan telah meningkatkan lagi kestabilan dan automasi proses pemotongan. Kemajuan ini mengurangkan ralat yang disebabkan oleh operasi manusia dan meningkatkan ketekalan pemotongan. Pengenalan pemeriksaan lanjutan dan teknologi kawalan kualiti untuk pemantauan masa nyata anomali semasa proses pemotongan juga telah meningkatkan kebolehpercayaan dan hasil pemotongan dengan ketara.
Pembangunan Masa Depan dan Teknologi Baharu
Walaupun teknologi pemotongan mekanikal masih memegang kedudukan penting dalam pemotongan wafer, teknologi pemotongan baharu berkembang pesat apabila proses semikonduktor berkembang. Sebagai contoh, aplikasi teknologi pemotongan laser haba menyediakan penyelesaian baharu kepada isu ketepatan dan kecacatan dalam pemotongan mekanikal. Kaedah pemotongan tanpa sentuhan ini mengurangkan tekanan fizikal pada wafer, dengan ketara mengurangkan kejadian kerepek dan retak, terutamanya apabila memotong lebih banyak bahan rapuh. Pada masa hadapan, penyepaduan teknologi pemotongan mekanikal dengan teknik pemotongan yang baru muncul akan menyediakan pembuatan semikonduktor dengan lebih banyak pilihan dan fleksibiliti, meningkatkan lagi kecekapan pembuatan dan kualiti cip.
Kesimpulannya, walaupun teknologi pemotongan mekanikal mempunyai kelemahan tertentu, penambahbaikan teknologi berterusan dan penyepaduannya dengan teknik pemotongan baharu membolehkannya masih memainkan peranan penting dalam pembuatan semikonduktor dan mengekalkan daya saingnya dalam proses masa hadapan.
2.2 Teknologi Pemotongan Laser
Teknologi pemotongan laser, sebagai kaedah baharu dalam pemotongan wafer, secara beransur-ansur mendapat perhatian meluas dalam industri semikonduktor kerana ketepatannya yang tinggi, kekurangan kerosakan sentuhan mekanikal, dan keupayaan pemotongan pantas. Teknologi ini menggunakan ketumpatan tenaga yang tinggi dan keupayaan memfokus pancaran laser untuk mencipta zon kecil yang terjejas haba pada permukaan bahan wafer. Apabila pancaran laser digunakan pada wafer, tegasan haba yang dijana menyebabkan bahan patah di lokasi yang ditetapkan, mencapai pemotongan yang tepat.
Kelebihan Teknologi Laser Cutting
• Ketepatan Tinggi: Keupayaan kedudukan tepat pancaran laser membolehkan ketepatan pemotongan tahap mikron atau nanometer, memenuhi keperluan pembuatan litar bersepadu berketepatan tinggi moden dan berketumpatan tinggi.
• Tiada Kenalan Mekanikal: Pemotongan laser mengelakkan sentuhan fizikal dengan wafer, menghalang isu biasa dalam pemotongan mekanikal, seperti kerepek dan retak, meningkatkan kadar hasil dan kebolehpercayaan cip dengan ketara.
• Kelajuan Pemotongan Pantas: Kelajuan tinggi pemotongan laser menyumbang kepada peningkatan kecekapan pengeluaran, menjadikannya sangat sesuai untuk senario pengeluaran berskala besar dan berkelajuan tinggi.
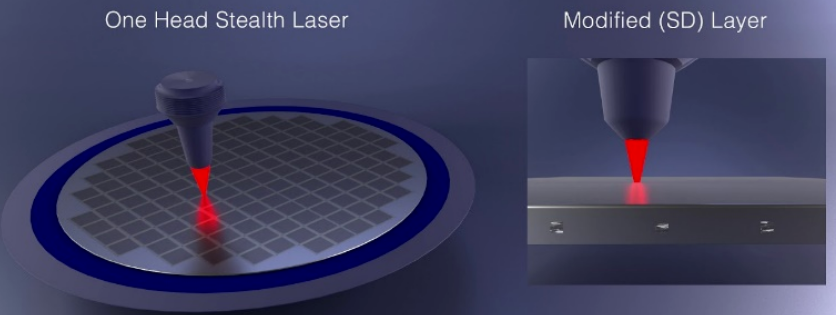
Cabaran Yang Dihadapi
• Kos Peralatan Tinggi: Pelaburan awal untuk peralatan pemotongan laser adalah tinggi, yang memberikan tekanan ekonomi, terutamanya untuk perusahaan pengeluaran kecil hingga sederhana.
• Kawalan Proses Kompleks: Pemotongan laser memerlukan kawalan tepat beberapa parameter, termasuk ketumpatan tenaga, kedudukan fokus, dan kelajuan pemotongan, menjadikan proses kompleks.
• Isu Zon Terjejas Haba: Walaupun sifat tidak bersentuhan pemotongan laser mengurangkan kerosakan mekanikal, tegasan haba yang disebabkan oleh zon terjejas haba (HAZ) boleh memberi kesan negatif kepada sifat bahan wafer. Pengoptimuman lanjut proses diperlukan untuk meminimumkan kesan ini.
Arah Penambahbaikan Teknologi
Untuk menangani cabaran ini, penyelidik menumpukan pada mengurangkan kos peralatan, meningkatkan kecekapan pemotongan, dan mengoptimumkan aliran proses.
• Laser dan Sistem Optik yang Cekap: Dengan membangunkan laser yang lebih cekap dan sistem optik termaju, adalah mungkin untuk mengurangkan kos peralatan sambil meningkatkan ketepatan dan kelajuan pemotongan.
• Mengoptimumkan Parameter Proses: Penyelidikan mendalam tentang interaksi antara laser dan bahan wafer sedang dijalankan untuk menambah baik proses yang mengurangkan zon terjejas haba, sekali gus meningkatkan kualiti pemotongan.
• Sistem Kawalan Pintar: Pembangunan teknologi kawalan pintar bertujuan untuk mengautomasikan dan mengoptimumkan proses pemotongan laser, meningkatkan kestabilan dan ketekalannya.
Teknologi pemotongan laser amat berkesan dalam wafer ultra nipis dan senario pemotongan berketepatan tinggi. Apabila saiz wafer meningkat dan ketumpatan litar meningkat, kaedah pemotongan mekanikal tradisional bergelut untuk memenuhi keperluan ketepatan tinggi dan kecekapan tinggi pembuatan semikonduktor moden. Disebabkan kelebihannya yang unik, pemotongan laser menjadi penyelesaian pilihan dalam bidang ini.
Walaupun teknologi pemotongan laser masih menghadapi cabaran seperti kos peralatan yang tinggi dan kerumitan proses, kelebihan uniknya dalam ketepatan tinggi dan kerosakan bukan sentuhan menjadikannya hala tuju penting untuk pembangunan dalam pembuatan semikonduktor. Memandangkan teknologi laser dan sistem kawalan pintar terus maju, pemotongan laser dijangka meningkatkan lagi kecekapan dan kualiti pemotongan wafer, memacu pembangunan berterusan industri semikonduktor.
2.3 Teknologi Pemotongan Plasma
Teknologi pemotongan plasma, sebagai kaedah pemotongan wafer yang baru muncul, telah mendapat perhatian yang ketara dalam beberapa tahun kebelakangan ini. Teknologi ini menggunakan rasuk plasma bertenaga tinggi untuk memotong wafer dengan tepat dengan mengawal tenaga, kelajuan dan laluan pemotongan rasuk plasma, mencapai hasil pemotongan yang optimum.
Prinsip Kerja dan Kelebihan
Proses pemotongan plasma bergantung pada pancaran plasma bersuhu tinggi dan bertenaga tinggi yang dihasilkan oleh peralatan. Rasuk ini boleh memanaskan bahan wafer ke titik lebur atau pengewapannya dalam masa yang sangat singkat, membolehkan pemotongan pantas. Berbanding dengan pemotongan mekanikal atau laser tradisional, pemotongan plasma lebih pantas dan menghasilkan zon terjejas haba yang lebih kecil, dengan berkesan mengurangkan kejadian retak dan kerosakan semasa pemotongan.
Dalam aplikasi praktikal, teknologi pemotongan plasma amat mahir dalam mengendalikan wafer dengan bentuk yang kompleks. Rasuk plasma boleh laras bertenaga tingginya boleh memotong wafer berbentuk tidak sekata dengan ketepatan tinggi dengan mudah. Oleh itu, dalam pembuatan mikroelektronik, terutamanya dalam pengeluaran cip mewah tersuai dan kecil, teknologi ini menunjukkan janji besar untuk kegunaan meluas.
Cabaran dan Had
Walaupun terdapat banyak kelebihan teknologi pemotongan plasma, ia juga menghadapi beberapa cabaran.
• Proses Kompleks: Proses pemotongan plasma adalah kompleks dan memerlukan peralatan berketepatan tinggi dan pengendali berpengalaman untuk memastikanketepatan dan kestabilan dalam pemotongan.
• Kawalan dan Keselamatan Alam Sekitar: Sifat pancaran plasma bersuhu tinggi dan bertenaga tinggi memerlukan kawalan alam sekitar yang ketat dan langkah keselamatan, yang meningkatkan kerumitan dan kos pelaksanaan.
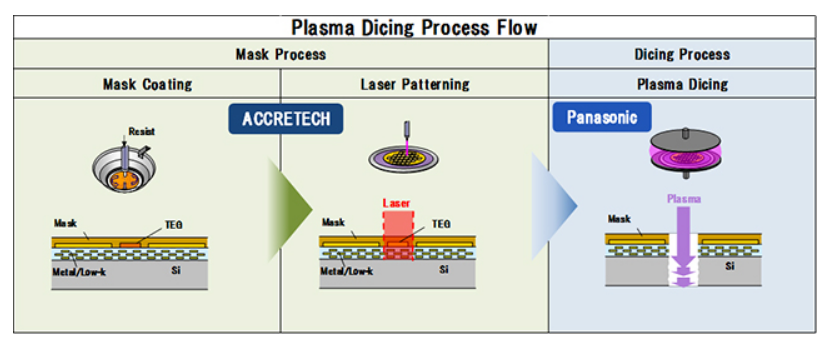
Arah Pembangunan Masa Depan
Dengan kemajuan teknologi, cabaran yang berkaitan dengan pemotongan plasma dijangka dapat diatasi secara beransur-ansur. Dengan membangunkan peralatan pemotongan yang lebih pintar dan lebih stabil, pergantungan pada operasi manual dapat dikurangkan, dengan itu meningkatkan kecekapan pengeluaran. Pada masa yang sama, mengoptimumkan parameter proses dan persekitaran pemotongan akan membantu mengurangkan risiko keselamatan dan kos operasi.
Dalam industri semikonduktor, inovasi dalam teknologi pemotongan wafer dan pemotongan dadu adalah penting untuk memacu pembangunan industri. Teknologi pemotongan plasma, dengan ketepatan tinggi, kecekapan dan keupayaannya untuk mengendalikan bentuk wafer yang kompleks, telah muncul sebagai pemain baharu yang penting dalam bidang ini. Walaupun beberapa cabaran kekal, isu ini akan ditangani secara beransur-ansur dengan inovasi teknologi yang berterusan, membawa lebih banyak kemungkinan dan peluang kepada pembuatan semikonduktor.
Prospek aplikasi teknologi pemotongan plasma adalah luas, dan ia dijangka memainkan peranan yang lebih penting dalam pembuatan semikonduktor pada masa hadapan. Melalui inovasi dan pengoptimuman teknologi berterusan, pemotongan plasma bukan sahaja akan menangani cabaran sedia ada tetapi juga menjadi pemacu kuat pertumbuhan industri semikonduktor.
2.4 Kualiti Pemotongan dan Faktor Mempengaruhi
Kualiti pemotongan wafer adalah penting untuk pembungkusan cip seterusnya, ujian, dan prestasi keseluruhan dan kebolehpercayaan produk akhir. Isu biasa yang dihadapi semasa pemotongan termasuk keretakan, serpihan dan sisihan pemotongan. Masalah ini dipengaruhi oleh beberapa faktor yang bekerjasama.
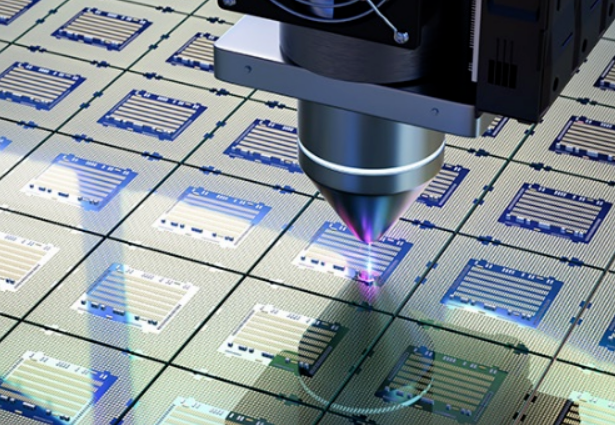
kategori | kandungan | Kesan |
Parameter Proses | Kelajuan pemotongan, kadar suapan, dan kedalaman pemotongan secara langsung mempengaruhi kestabilan dan ketepatan proses pemotongan. Tetapan yang tidak betul boleh menyebabkan kepekatan tegasan dan zon terjejas haba yang berlebihan, mengakibatkan keretakan dan serpihan. Melaraskan parameter dengan sewajarnya berdasarkan bahan wafer, ketebalan dan keperluan pemotongan adalah kunci untuk mencapai hasil pemotongan yang diingini. | Parameter proses yang betul memastikan pemotongan yang tepat dan mengurangkan risiko kecacatan seperti keretakan dan serpihan. |
Faktor Peralatan dan Bahan | -Kualiti Bilah: Bahan, kekerasan, dan rintangan haus bilah mempengaruhi kelancaran proses pemotongan dan kerataan permukaan potong. Bilah yang tidak berkualiti meningkatkan geseran dan tekanan haba, yang berpotensi menyebabkan keretakan atau serpihan. Memilih bahan bilah yang betul adalah penting. -Prestasi Penyejuk: Bahan penyejuk membantu mengurangkan suhu pemotongan, meminimumkan geseran dan membersihkan serpihan. Penyejuk yang tidak berkesan boleh menyebabkan suhu tinggi dan pengumpulan serpihan, menjejaskan kualiti dan kecekapan pemotongan. Memilih penyejuk yang cekap dan mesra alam adalah penting. | Kualiti bilah mempengaruhi ketepatan dan kelancaran potongan. Penyejuk yang tidak berkesan boleh mengakibatkan kualiti pemotongan dan kecekapan yang rendah, menyerlahkan keperluan untuk penggunaan penyejuk yang optimum. |
Kawalan Proses dan Pemeriksaan Kualiti | -Kawalan Proses: Pemantauan masa nyata dan pelarasan parameter pemotongan utama untuk memastikan kestabilan dan konsistensi dalam proses pemotongan. -Pemeriksaan Kualiti: Pemeriksaan penampilan selepas pemotongan, ukuran dimensi dan ujian prestasi elektrik membantu mengenal pasti dan menangani isu kualiti dengan segera, meningkatkan ketepatan dan ketekalan pemotongan. | Kawalan proses dan pemeriksaan kualiti yang betul membantu memastikan hasil pemotongan yang konsisten dan berkualiti tinggi dan pengesanan awal masalah yang berpotensi. |

Meningkatkan Kualiti Pemotongan
Meningkatkan kualiti pemotongan memerlukan pendekatan menyeluruh yang mengambil kira parameter proses, pemilihan peralatan dan bahan, kawalan proses dan pemeriksaan. Dengan terus memperhalusi teknologi pemotongan dan mengoptimumkan kaedah proses, ketepatan dan kestabilan pemotongan wafer boleh dipertingkatkan lagi, memberikan sokongan teknikal yang lebih dipercayai untuk industri pembuatan semikonduktor.
#03 Pengendalian dan Ujian Selepas Pemotongan
3.1 Pembersihan dan Pengeringan
Langkah pembersihan dan pengeringan selepas pemotongan wafer adalah penting untuk memastikan kualiti cip dan kelancaran proses seterusnya. Semasa peringkat ini, adalah penting untuk membuang serpihan silikon, sisa penyejuk dan bahan cemar lain yang dihasilkan semasa pemotongan. Sama pentingnya untuk memastikan bahawa cip tidak rosak semasa proses pembersihan, dan selepas pengeringan, pastikan tiada kelembapan kekal pada permukaan cip untuk mengelakkan isu seperti kakisan atau nyahcas elektrostatik.
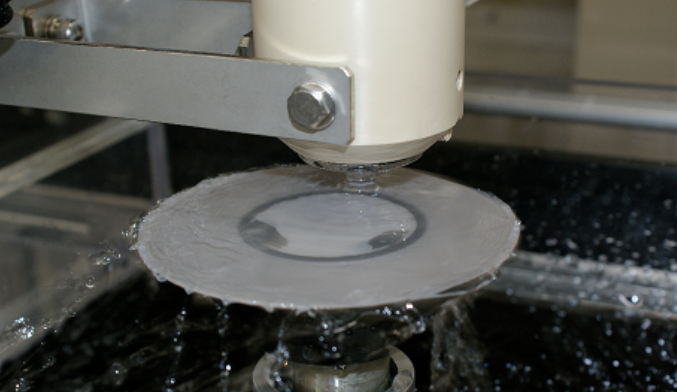
Pengendalian Selepas Memotong: Proses Pembersihan dan Pengeringan
Langkah Proses | kandungan | Kesan |
Proses Pembersihan | -Kaedah: Gunakan agen pembersih khusus dan air tulen, digabungkan dengan teknik memberus ultrasonik atau mekanikal untuk pembersihan. | Memastikan penyingkiran bahan cemar secara menyeluruh dan mengelakkan kerosakan pada cip semasa pembersihan. |
-Pemilihan Ejen Pembersihan: Pilih berdasarkan bahan wafer dan jenis pencemar untuk memastikan pembersihan yang berkesan tanpa merosakkan cip. | Pemilihan ejen yang betul adalah kunci untuk pembersihan yang berkesan dan perlindungan cip. | |
-Kawalan Parameter: Kawal ketat suhu pembersihan, masa dan kepekatan larutan pembersihan untuk mengelakkan isu kualiti yang disebabkan oleh pembersihan yang tidak betul. | Kawalan membantu mengelak daripada merosakkan wafer atau meninggalkan bahan cemar, memastikan kualiti yang konsisten. | |
Proses Pengeringan | -Kaedah Tradisional: Pengeringan udara semula jadi dan pengeringan udara panas, yang mempunyai kecekapan yang rendah dan boleh menyebabkan pembentukan elektrik statik. | Boleh mengakibatkan masa pengeringan yang lebih perlahan dan kemungkinan isu statik. |
-Teknologi Moden: Gunakan teknologi canggih seperti pengeringan vakum dan pengeringan inframerah untuk memastikan cip kering dengan cepat dan mengelakkan kesan berbahaya. | Proses pengeringan yang lebih pantas dan cekap, mengurangkan risiko pelepasan statik atau isu berkaitan kelembapan. | |
Pemilihan & Penyelenggaraan Peralatan | -Pemilihan Peralatan: Mesin pembersihan dan pengeringan berprestasi tinggi meningkatkan kecekapan pemprosesan dan mengawal masalah berpotensi semasa pengendalian. | Mesin berkualiti tinggi memastikan pemprosesan yang lebih baik dan mengurangkan kemungkinan ralat semasa pembersihan dan pengeringan. |
-Penyelenggaraan Peralatan: Pemeriksaan dan penyelenggaraan yang kerap peralatan memastikan ia kekal dalam keadaan kerja yang optimum, menjamin kualiti cip. | Penyelenggaraan yang betul menghalang kegagalan peralatan, memastikan pemprosesan yang boleh dipercayai dan berkualiti tinggi. |
Pembersihan dan Pengeringan Selepas Memotong
Langkah-langkah pembersihan dan pengeringan selepas pemotongan wafer adalah proses yang rumit dan halus yang memerlukan pertimbangan teliti pelbagai faktor untuk memastikan hasil pemprosesan akhir. Dengan menggunakan kaedah saintifik dan prosedur yang ketat, adalah mungkin untuk memastikan setiap cip memasuki peringkat pembungkusan dan ujian seterusnya dalam keadaan optimum.
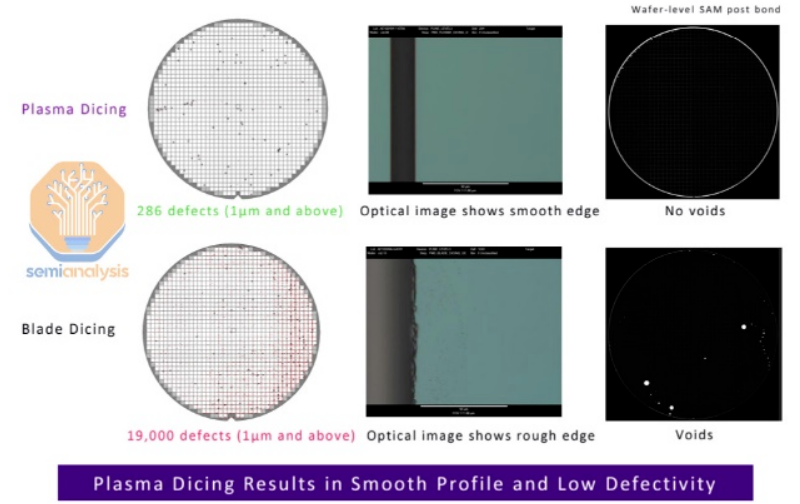
Pemeriksaan dan Ujian Selepas Pemotongan
Langkah | kandungan | Kesan |
Langkah Pemeriksaan | 1.Pemeriksaan Visual: Gunakan peralatan pemeriksaan visual atau automatik untuk memeriksa kecacatan yang boleh dilihat seperti keretakan, serpihan atau pencemaran pada permukaan cip. Kenal pasti cip yang rosak secara fizikal dengan cepat untuk mengelakkan pembaziran. | Membantu dalam mengenal pasti dan menghapuskan cip yang rosak pada awal proses, mengurangkan kehilangan bahan. |
2.Ukuran Saiz: Gunakan peranti pengukur ketepatan untuk mengukur dimensi cip dengan tepat, memastikan saiz potongan memenuhi spesifikasi reka bentuk dan mencegah isu prestasi atau kesukaran pembungkusan. | Memastikan cip berada dalam had saiz yang diperlukan, menghalang kemerosotan prestasi atau masalah pemasangan. | |
3.Ujian Prestasi Elektrik: Nilaikan parameter elektrik utama seperti rintangan, kapasitansi dan kearuhan, untuk mengenal pasti cip yang tidak mematuhi dan memastikan hanya cip yang memenuhi syarat prestasi meneruskan ke peringkat seterusnya. | Memastikan hanya cip yang berfungsi dan diuji prestasi bergerak ke hadapan dalam proses, mengurangkan risiko kegagalan pada peringkat seterusnya. | |
Langkah Pengujian | 1.Ujian Fungsian: Sahkan bahawa kefungsian asas cip berfungsi seperti yang dimaksudkan, mengenal pasti dan menghapuskan cip dengan keabnormalan fungsi. | Memastikan cip memenuhi keperluan operasi asas sebelum maju ke peringkat seterusnya. |
2.Ujian Kebolehpercayaan: Nilaikan kestabilan prestasi cip di bawah penggunaan berpanjangan atau persekitaran yang keras, biasanya melibatkan penuaan suhu tinggi, ujian suhu rendah dan ujian kelembapan untuk mensimulasikan keadaan melampau dunia sebenar. | Memastikan cip boleh berfungsi dengan pasti di bawah pelbagai keadaan persekitaran, meningkatkan umur panjang dan kestabilan produk. | |
3.Ujian Keserasian: Sahkan bahawa cip berfungsi dengan baik dengan komponen atau sistem lain, memastikan tiada kerosakan atau penurunan prestasi akibat ketidakserasian. | Memastikan operasi lancar dalam aplikasi dunia sebenar dengan menghalang isu keserasian. |
3.3 Pembungkusan dan Penyimpanan
Selepas pemotongan wafer, cip adalah keluaran penting dalam proses pembuatan semikonduktor, dan peringkat pembungkusan dan penyimpanannya adalah sama penting. Langkah pembungkusan dan penyimpanan yang betul adalah penting bukan sahaja untuk memastikan keselamatan dan kestabilan cip semasa pengangkutan dan penyimpanan tetapi juga untuk menyediakan sokongan kuat untuk peringkat pengeluaran, ujian dan pembungkusan seterusnya.
Ringkasan Peringkat Pemeriksaan dan Pengujian:
Langkah-langkah pemeriksaan dan ujian untuk cip selepas pemotongan wafer meliputi pelbagai aspek, termasuk pemeriksaan visual, ukuran saiz, ujian prestasi elektrik, ujian kefungsian, ujian kebolehpercayaan dan ujian keserasian. Langkah-langkah ini saling berkaitan dan saling melengkapi, membentuk penghalang yang kukuh untuk memastikan kualiti dan kebolehpercayaan produk. Melalui prosedur pemeriksaan dan ujian yang ketat, isu yang berpotensi dapat dikenal pasti dan diselesaikan dengan segera, memastikan produk akhir memenuhi keperluan dan jangkaan pelanggan.
Aspek | kandungan |
Langkah Pembungkusan | 1.Anti statik: Bahan pembungkusan harus mempunyai sifat anti-statik yang sangat baik untuk mengelakkan elektrik statik daripada merosakkan peranti atau menjejaskan prestasinya. |
2.Kalis lembapan: Bahan pembungkusan harus mempunyai rintangan lembapan yang baik untuk mengelakkan kakisan dan kemerosotan prestasi elektrik yang disebabkan oleh kelembapan. | |
3.Kalis kejutan: Bahan pembungkusan harus menyediakan penyerapan kejutan yang berkesan untuk melindungi cip daripada getaran dan hentaman semasa pengangkutan. | |
Persekitaran Storan | 1.Kawalan Kelembapan: Kawal kelembapan dengan ketat dalam julat yang sesuai untuk mengelakkan penyerapan lembapan dan kakisan yang disebabkan oleh kelembapan berlebihan atau isu statik yang disebabkan oleh kelembapan yang rendah. |
2.Kebersihan: Kekalkan persekitaran penyimpanan yang bersih untuk mengelakkan pencemaran cip oleh habuk dan kekotoran. | |
3.Kawalan Suhu: Tetapkan julat suhu yang munasabah dan kekalkan kestabilan suhu untuk mengelakkan penuaan dipercepatkan akibat haba yang berlebihan atau masalah pemeluwapan yang disebabkan oleh suhu rendah. | |
Pemeriksaan Berkala | Periksa dan nilai cip yang disimpan secara kerap, menggunakan pemeriksaan visual, ukuran saiz dan ujian prestasi elektrik untuk mengenal pasti dan menangani isu yang berpotensi tepat pada masanya. Berdasarkan masa dan keadaan penyimpanan, rancang penggunaan cip untuk memastikan ia digunakan dalam keadaan optimum. |
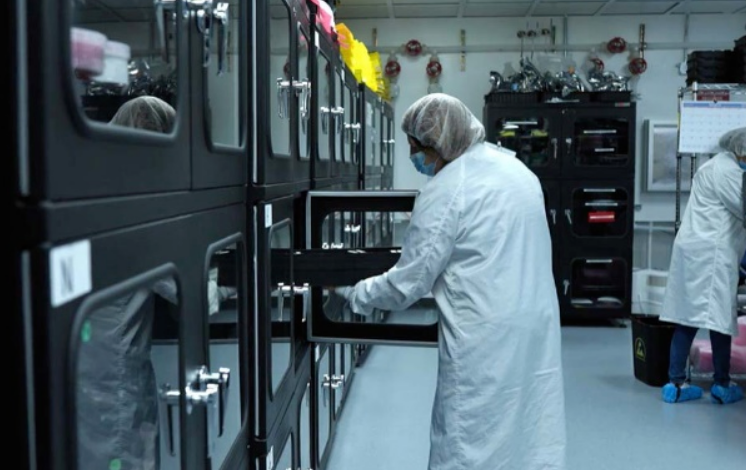
Isu retakan mikro dan kerosakan semasa proses pemotongan wafer merupakan cabaran yang ketara dalam pembuatan semikonduktor. Tekanan pemotongan adalah punca utama fenomena ini, kerana ia mewujudkan keretakan kecil dan kerosakan pada permukaan wafer, yang membawa kepada peningkatan kos pembuatan dan penurunan dalam kualiti produk.
Untuk menangani cabaran ini, adalah penting untuk meminimumkan tekanan pemotongan dan melaksanakan teknik pemotongan yang dioptimumkan, alatan dan keadaan. Perhatian yang teliti terhadap faktor seperti bahan bilah, kelajuan pemotongan, tekanan, dan kaedah penyejukan boleh membantu mengurangkan pembentukan retakan mikro dan meningkatkan hasil keseluruhan proses. Selain itu, penyelidikan berterusan ke dalam teknologi pemotongan yang lebih maju, seperti pemotongan laser, sedang meneroka cara untuk mengurangkan lagi isu ini.
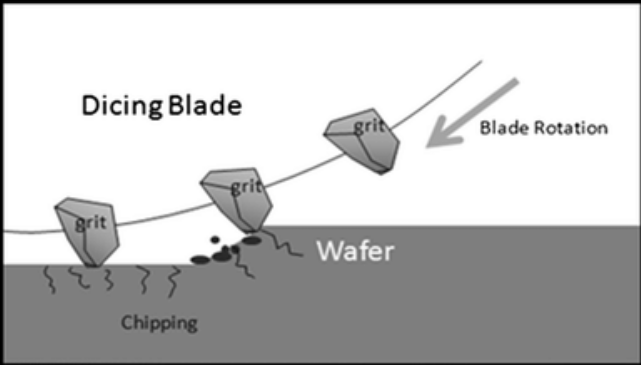
Sebagai bahan yang rapuh, wafer terdedah kepada perubahan struktur dalaman apabila tertakluk kepada tekanan mekanikal, haba atau kimia, yang membawa kepada pembentukan retakan mikro. Walaupun keretakan ini mungkin tidak dapat dilihat dengan segera, ia boleh mengembang dan menyebabkan kerosakan yang lebih teruk apabila proses pembuatan berlangsung. Isu ini menjadi sangat bermasalah semasa peringkat pembungkusan dan ujian berikutnya, di mana turun naik suhu dan tegasan mekanikal tambahan boleh menyebabkan retakan mikro ini berkembang menjadi patah yang boleh dilihat, yang berpotensi membawa kepada kegagalan cip.
Untuk mengurangkan risiko ini, adalah penting untuk mengawal proses pemotongan dengan berhati-hati dengan mengoptimumkan parameter seperti kelajuan pemotongan, tekanan dan suhu. Menggunakan kaedah pemotongan yang kurang agresif, seperti pemotongan laser, boleh mengurangkan tekanan mekanikal pada wafer dan meminimumkan pembentukan retakan mikro. Selain itu, melaksanakan kaedah pemeriksaan lanjutan seperti pengimbasan inframerah atau pengimejan sinar-X semasa proses dadu wafer boleh membantu mengesan keretakan peringkat awal ini sebelum menyebabkan kerosakan selanjutnya.
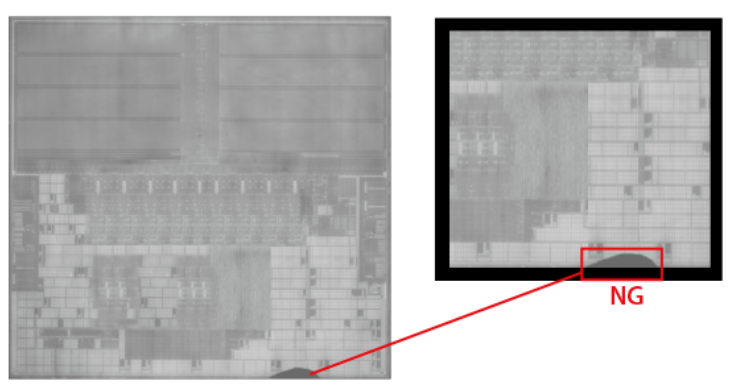
Kerosakan pada permukaan wafer adalah kebimbangan yang ketara dalam proses pemotongan dadu, kerana ia boleh memberi kesan langsung kepada prestasi dan kebolehpercayaan cip. Kerosakan sedemikian boleh disebabkan oleh penggunaan alat pemotong yang tidak betul, parameter pemotongan yang salah, atau kecacatan bahan yang wujud dalam wafer itu sendiri. Tanpa mengira puncanya, kerosakan ini boleh menyebabkan perubahan pada rintangan elektrik atau kapasitansi litar, yang menjejaskan prestasi keseluruhan.
Untuk menangani isu ini, dua strategi utama sedang diterokai:
1. Mengoptimumkan alat pemotong dan parameter: Dengan menggunakan bilah yang lebih tajam, melaraskan kelajuan pemotongan, dan mengubah suai kedalaman pemotongan, kepekatan tegasan semasa proses pemotongan dapat diminimumkan, sekali gus mengurangkan potensi kerosakan.
2. Meneroka teknologi pemotongan baharu: Teknik lanjutan seperti pemotongan laser dan pemotongan plasma menawarkan ketepatan yang lebih baik sambil berpotensi mengurangkan tahap kerosakan yang dikenakan pada wafer. Teknologi ini sedang dikaji untuk mencari cara untuk mencapai ketepatan pemotongan yang tinggi sambil meminimumkan tekanan terma dan mekanikal pada wafer.
Kawasan Kesan Terma dan Kesannya terhadap Prestasi
Dalam proses pemotongan haba seperti pemotongan laser dan plasma, suhu tinggi tidak dapat dielakkan mewujudkan zon impak haba pada permukaan wafer. Kawasan ini, di mana kecerunan suhu adalah ketara, boleh mengubah sifat bahan, menjejaskan prestasi akhir cip.
Kesan Zon Terjejas Terma (TAZ):
Perubahan Struktur Kristal: Di bawah suhu tinggi, atom dalam bahan wafer mungkin tersusun semula, menyebabkan herotan dalam struktur kristal. Herotan ini melemahkan bahan, mengurangkan kekuatan mekanikal dan kestabilannya, yang meningkatkan risiko kegagalan cip semasa penggunaan.
Perubahan dalam Sifat Elektrik: Suhu tinggi boleh mengubah kepekatan pembawa dan mobiliti dalam bahan semikonduktor, menjejaskan kekonduksian elektrik cip dan kecekapan penghantaran arus. Perubahan ini boleh menyebabkan penurunan prestasi cip, yang berpotensi menjadikannya tidak sesuai untuk tujuan yang dimaksudkan.
Untuk mengurangkan kesan ini, mengawal suhu semasa pemotongan, mengoptimumkan parameter pemotongan, dan meneroka kaedah seperti jet penyejukan atau rawatan pasca pemprosesan adalah strategi penting untuk mengurangkan tahap kesan haba dan mengekalkan integriti bahan.
Secara keseluruhan, kedua-dua microcracks dan zon impak haba adalah cabaran penting dalam teknologi dadu wafer. Penyelidikan yang berterusan, di samping kemajuan teknologi dan langkah kawalan kualiti, akan diperlukan untuk meningkatkan kualiti produk semikonduktor dan meningkatkan daya saing pasaran mereka.
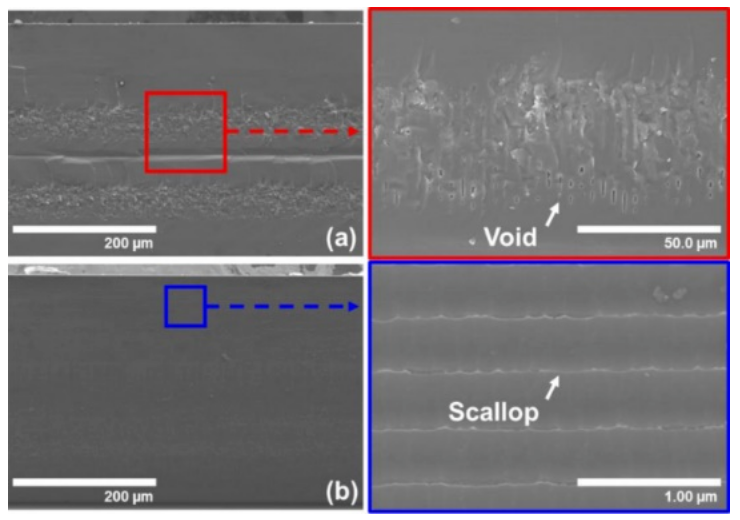
Langkah-langkah untuk Mengawal Zon Kesan Terma:
Mengoptimumkan Parameter Proses Pemotongan: Mengurangkan kelajuan pemotongan dan kuasa boleh meminimumkan saiz zon hentaman haba (TAZ) dengan berkesan. Ini membantu dalam mengawal jumlah haba yang dijana semasa proses pemotongan, yang secara langsung memberi kesan kepada sifat bahan wafer.
Teknologi Penyejukan Termaju: Aplikasi teknologi seperti penyejukan nitrogen cecair dan penyejukan mikrobendalir boleh mengehadkan julat zon hentaman haba dengan ketara. Kaedah penyejukan ini membantu menghilangkan haba dengan lebih cekap, sekali gus memelihara sifat bahan wafer dan meminimumkan kerosakan haba.
Pemilihan Bahan: Penyelidik sedang meneroka bahan baharu, seperti tiub nano karbon dan graphene, yang mempunyai kekonduksian terma dan kekuatan mekanikal yang sangat baik. Bahan-bahan ini boleh mengurangkan zon hentaman haba sambil meningkatkan prestasi keseluruhan cip.
Ringkasnya, walaupun zon hentaman haba adalah akibat yang tidak dapat dielakkan daripada teknologi pemotongan haba, ia boleh dikawal dengan berkesan melalui teknik pemprosesan yang dioptimumkan dan pemilihan bahan. Penyelidikan masa depan mungkin akan menumpukan pada penalaan halus dan mengautomasikan proses pemotongan haba untuk mencapai dadu wafer yang lebih cekap dan tepat.

Strategi Imbangan:
Mencapai keseimbangan optimum antara hasil wafer dan kecekapan pengeluaran adalah cabaran berterusan dalam teknologi dadu wafer. Pengilang perlu mempertimbangkan pelbagai faktor, seperti permintaan pasaran, kos pengeluaran dan kualiti produk, untuk membangunkan strategi pengeluaran dan parameter proses yang rasional. Pada masa yang sama, memperkenalkan peralatan pemotongan termaju, meningkatkan kemahiran pengendali, dan meningkatkan kawalan kualiti bahan mentah adalah penting untuk mengekalkan atau bahkan meningkatkan hasil sambil meningkatkan kecekapan pengeluaran.
Cabaran dan Peluang Masa Depan:
Dengan kemajuan teknologi semikonduktor, pemotongan wafer menghadapi cabaran dan peluang baharu. Apabila saiz cip mengecil dan penyepaduan meningkat, permintaan terhadap ketepatan pemotongan dan kualiti meningkat dengan ketara. Pada masa yang sama, teknologi baru muncul memberikan idea baharu untuk pembangunan teknik pemotongan wafer. Pengilang mesti sentiasa selaras dengan dinamik pasaran dan trend teknologi, melaraskan dan mengoptimumkan strategi pengeluaran dan parameter proses secara berterusan untuk memenuhi perubahan pasaran dan permintaan teknologi.
Kesimpulannya, dengan menyepadukan pertimbangan permintaan pasaran, kos pengeluaran dan kualiti produk, dan dengan memperkenalkan peralatan dan teknologi canggih, meningkatkan kemahiran pengendali, dan mengukuhkan kawalan bahan mentah, pengilang boleh mencapai keseimbangan terbaik antara hasil wafer dan kecekapan pengeluaran semasa pemotongan wafer, yang membawa kepada pengeluaran produk semikonduktor yang cekap dan berkualiti tinggi.
Tinjauan Masa Depan:
Dengan kemajuan teknologi yang pesat, teknologi semikonduktor berkembang pada kadar yang tidak pernah berlaku sebelum ini. Sebagai langkah kritikal dalam pembuatan semikonduktor, teknologi pemotongan wafer bersedia untuk perkembangan baharu yang menarik. Memandang ke hadapan, teknologi pemotongan wafer dijangka mencapai peningkatan ketara dalam ketepatan, kecekapan dan kos, menyuntik tenaga baharu ke dalam pertumbuhan berterusan industri semikonduktor.
Meningkatkan Ketepatan:
Dalam mengejar ketepatan yang lebih tinggi, teknologi pemotongan wafer akan terus menolak had proses sedia ada. Dengan mengkaji secara mendalam mekanisme fizikal dan kimia proses pemotongan dan mengawal parameter pemotongan dengan tepat, hasil pemotongan yang lebih halus akan dicapai untuk memenuhi keperluan reka bentuk litar yang semakin kompleks. Selain itu, penerokaan bahan baharu dan kaedah pemotongan akan meningkatkan hasil dan kualiti dengan ketara.
Meningkatkan Kecekapan:
Peralatan pemotongan wafer baharu akan memberi tumpuan kepada reka bentuk pintar dan automatik. Pengenalan sistem kawalan dan algoritma lanjutan akan membolehkan peralatan melaraskan parameter pemotongan secara automatik untuk menampung keperluan bahan dan reka bentuk yang berbeza, sekali gus meningkatkan kecekapan pengeluaran dengan ketara. Inovasi seperti teknologi pemotongan berbilang wafer dan sistem penggantian bilah pantas akan memainkan peranan penting dalam meningkatkan kecekapan.
Mengurangkan Kos:
Mengurangkan kos adalah hala tuju utama untuk pembangunan teknologi pemotongan wafer. Apabila bahan baharu dan kaedah pemotongan dibangunkan, kos peralatan dan perbelanjaan penyelenggaraan dijangka dikawal dengan berkesan. Selain itu, mengoptimumkan proses pengeluaran dan mengurangkan kadar sekerap akan mengurangkan lagi sisa semasa pembuatan, yang membawa kepada penurunan kos pengeluaran keseluruhan.
Pembuatan Pintar dan IoT:
Penyepaduan pembuatan pintar dan teknologi Internet of Things (IoT) akan membawa perubahan transformatif kepada teknologi pemotongan wafer. Melalui kesalinghubungan dan perkongsian data antara peranti, setiap langkah proses pengeluaran boleh dipantau dan dioptimumkan dalam masa nyata. Ini bukan sahaja meningkatkan kecekapan pengeluaran dan kualiti produk tetapi juga menyediakan syarikat dengan ramalan pasaran yang lebih tepat dan sokongan membuat keputusan.
Pada masa hadapan, teknologi pemotongan wafer akan membuat kemajuan yang luar biasa dalam ketepatan, kecekapan dan kos. Kemajuan ini akan memacu pembangunan berterusan industri semikonduktor dan membawa lebih banyak inovasi dan kemudahan teknologi kepada masyarakat manusia.
Masa siaran: Nov-19-2024